K1
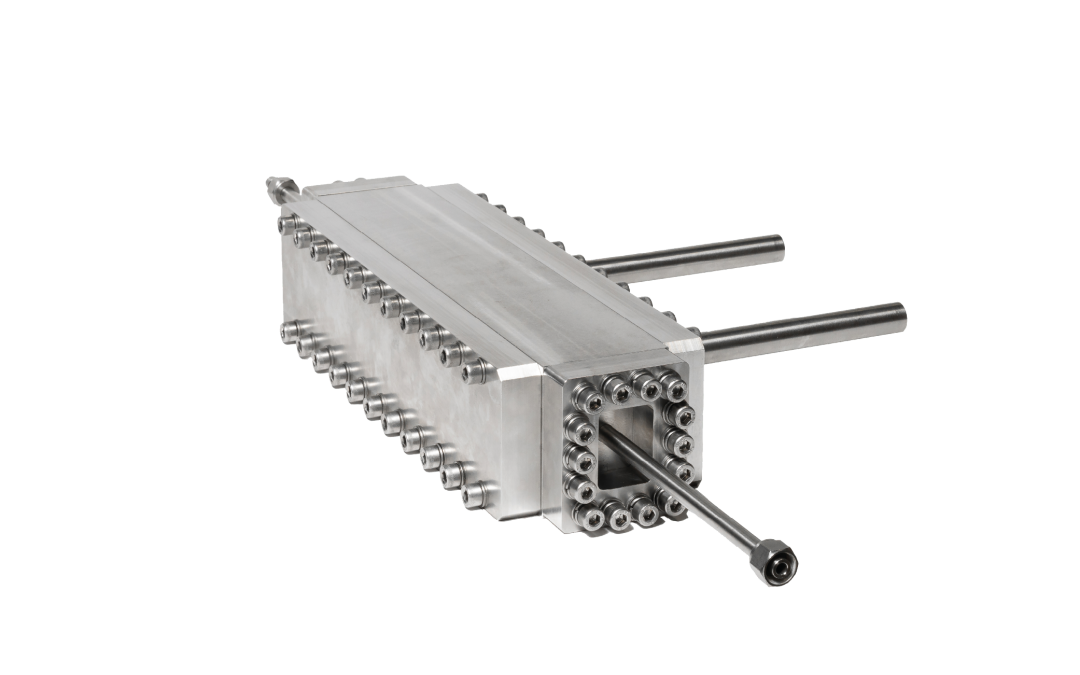
Most of the chemicals made for the fine or specialty chemical industry are made in batch.
Flow chemistry is the solution to optimize production for fine and specialty chemical industry.
Flow chemistry enables to manage safely very exothermic reactions thanks to an outstanding thermal exchange
Flow chemistry can be a solution when impurities or low yield are coming from a weak control of the temperature or reaction time
Challenging but KHIMOD can be the solution, with our patented technology coupling our reactor and ultrasounds
Handling gases, specially at high pressure, is challenging in batch but can be performed safely in flow
Flow chemistry enables to handle very hazardous intermediates safely by reducing the reactive volume
By using flow chemistry and process intensification approach, reaction time can be dramatically reduced
Faster
Safer
Greener
Better
More Cost
Effective
Configuration can be easily modified by changing the end caps
Opportunity to heat or cool the reagents before the reaction
Easy cleaning making it suitable for a multi-purpose workshop
Reactive channel length adjusted to the required residence time
A range of reactors addressing the need of the chemical industry for process intensification.
Identical design, from lab to full industrial scale, enabling a seamless scale-up.
Channel diameter and length: 6 mm and 30 cm.
From 12 to 784 reactive channels.
KHIMOD’s heat exchanger-reactors deliver outstanding performances on flow hydrogenation with fixed bed catalysts as illustrated in the following examples: